Surface Roughness Fabrication Methods
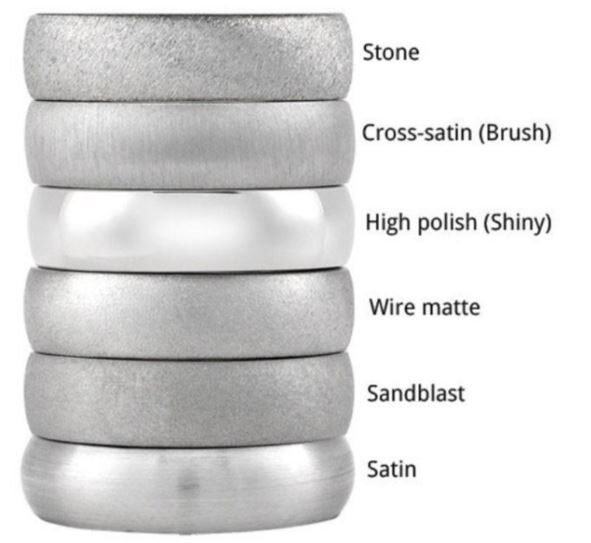
Reference website https://www.foen-group.com/uploads/%E5%9B%BE%E7%89%871.png
Surface roughness significantly influences various mechanical properties and functionalities, such as friction, wear resistance, and sealing capabilities. Below are relevant pieces of information regarding the achievable fabrication methods:
Fabrication Methods
1. Mechanical Machining:
Mechanical machining processes such as milling, grinding, boring, and polishing can control surface roughness to a certain extent. For example, grinding often achieves a finer surface roughness.
2. Chemical Treatment:
Some chemical treatment methods can alter the surface structure and chemical properties of metals, thereby adjusting their roughness. Examples include acid etching, electroplating, and chemical polishing.
3. Heat Treatment:
By controlling the heating and cooling processes of metals, it is possible to change their grain structure and surface properties, thereby affecting surface roughness.
4. Surface Finishing:
This includes methods such as coloring, painting, anodizing, etc., which not only change the appearance of metal surfaces but also allow for adjustments in surface roughness.
5. 3D Printing Technologies:
Different 3D printing techniques (such as selective laser melting, electron beam melting, etc.) can control the surface roughness of metal parts. Adjustments in printing parameters and post-processing methods can achieve various roughness requirements.
When fabricating metal parts, the choice of the most suitable fabrication method to control surface roughness is typically based on specific application requirements and cost considerations.
If your product has surface roughness requirements, please ensure that the surface roughness specifications (Ra) are included in your drawing.
Reference website https://an-prototype.com/wp-content/uploads/2023/09/Comparison-between-different-surface-roughnesses.png
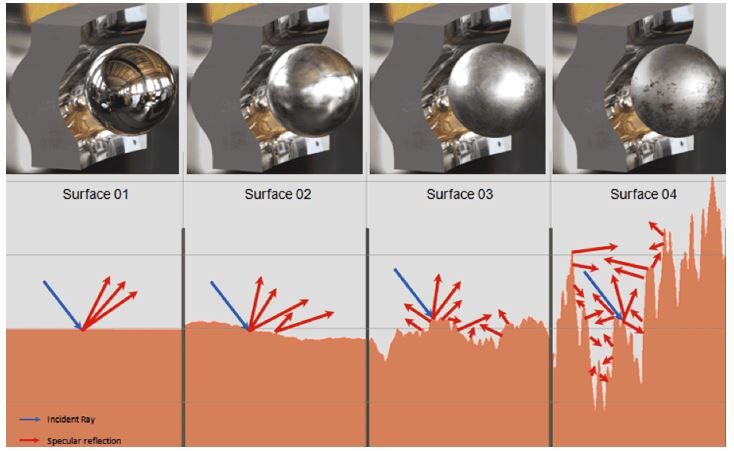