CNC lathe processing has been increasingly used in modern manufacturing, and CNC lathe processing has given play to the incomparable advantages of ordinary lathes. CNC lathe processing mainly has the following characteristics:
- The CNC lathe has a short transmission chain. Compared with ordinary lathes, the spindle drive is no longer driven by a motor belt and gear pair mechanism. Instead, the horizontal and vertical feeds are driven by two servo motors, and no hanging wheels and clutches are used.
And other traditional components, the transmission chain is greatly shortened. - High rigidity, which matches the high precision of CNC Machine and CNC system, and the high rigidity of CNC lathe processing in order to meet the high-precision processing requirements.
- Gently drag, the tool holder (table) moves using a ball screw pair, with low friction and easy movement. The support-type special bearings at both ends of the lead screw have a larger pressure angle than ordinary bearings and are selected when they leave the factory.
The lubricating part processed by CNC lathes is automatically lubricated by oil mist, these measures make CNC lathes easy to move.
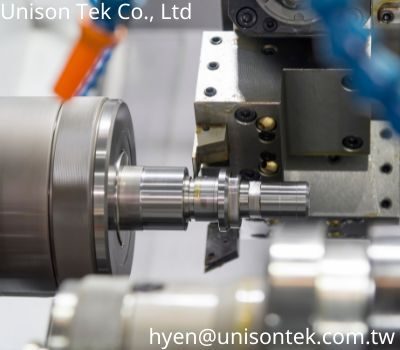
Second, CNC Lathe Processing Characteristics
- The high degree of automation can reduce the operator's manual labor intensity. The machining process of the CNC lathe is automatically completed according to the input program. The operator only needs to start the tool setting, load and unload the workpiece, and replace the tool.
During the machining process, the main purpose is to observe and supervise the operation of the lathe. However, due to the high technical content of CNC lathes, the operator's mental work is correspondingly improved. - CNC lathes process parts with high precision and stable quality. The positioning accuracy and repeated positioning accuracy of CNC lathes are very high, and it is easier to ensure the consistency of the size of a batch of parts.
As long as the process design and procedures are correct and reasonable, and careful operation, the parts can be guaranteed to obtain high machining accuracy, and it is also easy to adjust. Quality control is implemented in the machining process of CNC lathes. - CNC lathe has high production efficiency. CNC lathe processing can process multiple machined surfaces in one clamping, generally only the first piece is detected, so it can save many intermediate processes in ordinary lathe processing, such as scribing, size detection, etc., reducing auxiliary time.
And because the quality of the parts processed by the CNC lathe is stable, it brings convenience to the subsequent processes, and its overall efficiency is significantly improved. - CNC lathe processing facilitates the development and modification of new products. CNC lathe processing generally does not require a lot of complex process equipment.
By compiling processing programs, parts with complex shapes and high precision requirements can be processed. When the product is remodeled or the design is changed, only the program needs to be changed without redesigning. Tooling.
Therefore, CNC lathe processing can greatly shorten the product development cycle and provide a shortcut for the research and development of new products, product improvement, and modification. - CNC lathe processing can be developed to more advanced manufacturing systems. CNC lathe processing and its processing technology are the basis of computer-aided manufacturing.
- The initial investment of CNC lathe processing is relatively large. This is due to the high cost of CNC lathe processing equipment, a long preparation cycle for the first processing, and high maintenance costs.
- CNC lathes have high processing and maintenance requirements. CNC lathe is a typical CNC lathe processing product with technology-intensive mechatronics.
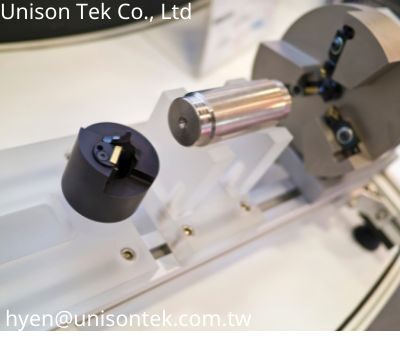
Parts suitable for CNC Lathe Processing
- CNC lathe processing is most suitable for multi-variety small and medium batch parts. With the gradual decline of the processing and manufacturing cost of CNC lathes, the situation of processing large quantities of parts has also appeared, whether at home or abroad.
When processing small batches and single-piece production, it is also possible to shorten the debugging time of the program and the preparation time of the tooling. - CNC lathe machining parts with high precision requirements. The CNC lathe has good rigidity, high manufacturing precision, accurate tool setting, and can easily perform dimensional compensation, so it can process parts with high dimensional accuracy requirements.
- CNC lathes process parts with small surface roughness values. In the case of constant workpiece and tool material, finishing allowance and tool angle, the surface roughness depends on the cutting speed and feed rate. Ordinary lathes have a constant rotation speed, and the cutting speed is different with different diameters.
For example, CNC numerical control lathes have a constant line speed cutting function.
The same line speed can be used when turning end faces and external circles with different diameters to ensure that the surface roughness value is small and consistent.
When machining surfaces with different surface roughness, a small feed rate is selected for the surface with small roughness, and a larger feed rate is selected for the surface with large roughness, and the variability is very good, which is difficult to achieve in ordinary lathes.
- Parts with complex contour shapes. Any plane curve can be approximated by a straight line or a circular arc, and the CNC lathe machining has the function of circular interpolation, which can process various complex contour bearing parts.
Fourth, The Management and Use of CNC Lathe Processing
The quality of CNC lathe processing requires not only the careful use of the operator, but also scientific management. A sound management system and a scientific production model are effective means to improve production efficiency.
- Establish a sound management system, effectively control and supervise the work of the relevant personnel of the CNC lathe, so that the operation and operation of the lathe can be controlled throughout the process.
- Strengthen the training of technical personnel and skilled worker management personnel. The training of CNC machining is a long-term work and a process of continuous improvement.
By training technicians, a more simplified CNC machining process can be programmed, programs can be simplified, and processing time can be shortened; skilled workers can improve operating skills.
Managers can better understand the characteristics of CNC equipment, process control, and implement management with modern production management concepts. - Scientific organization of production. Improve the problem of downtime and unbalanced production capacity, improve the operating rate of CNC lathe processing, reasonably arrange the production rhythm, and reasonably allocate production tasks.
Use the similarity of parts processing to classify the parts to be processed, so as to make reasonable arrangements in process preparation, production planning and scheduling, and improve the balance of equipment production capacity.Scientific production batches will greatly reduce the proportion of lathe adjustment time and tooling preparation time, which can improve batch efficiency.
- In order to give full play to the value of CNC lathe processing, the operator must correctly grasp the operating principles of CNC lathes.
Conclusion
The application of CNC lathe processing has become increasingly widespread, and how to "manage, use and maintain" CNC lathes has become an important issue to be solved urgently.
The use of CNC lathe and milling cutter processing is not a simple use of equipment, but an application project with strong sequential attributes.
Only by scientific management, fully understanding the characteristics of CNC lathe processing, and coordinating the balance of various production links, can it truly exert its economic benefits.
See our Facility and Inspection Equipment