In general, extrusion process falls into two basic categories, direct and indirect methods, which are what we usually use in aluminum industries. Solid and hollow extruded aluminum products are obtained after aluminum is extruded out of a die for a variety of purposes.
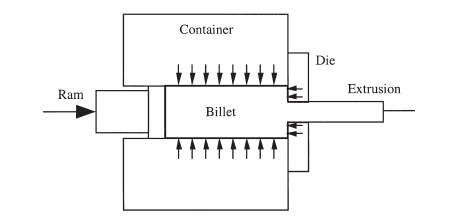
- Solid and concrete aluminum sections are extruded from solid billets through direct extrusion.
- Hollow aluminum sections are going through port-hole and bridge-like dies.
- Tube-like hollow sections are extruded from hollow or solid billets.
- Major solid sections or rods are extruded out of solid billets with airtight housings through the die by indirect extrusion process.
Conventional Direct Extrusion
The most commonly used method in aluminum extrusion is the principle of direct process, where the billet is set in the housing and forced through the die by the ram pressure.
Applications of direct aluminum extrusion can be found in the manufacture of concrete rods, bars, hollow tubes based on the design and shape of the die. During direct extrusion, metal travels in the same direction as the ram goes.
Therefore, frictional force results and then increase the ram pressure substantially. Basically, direct process involves three separate regions.
- The billet is upset, and pressure rises rapidly to its peak value.
- The pressure decreases, and what is termed “steady state” extrusion
proceeds.
- The pressure reaches its minimum value followed by a sharp rise as the “residue” is compacted.
Billet-on-Billet Extrusion
Billet-on-billet extrusion serves to weld aluminum alloys together at the extrusion temperature and pressure. During the process, uninterrupted lengths of a designated shape can be formed by different ways.
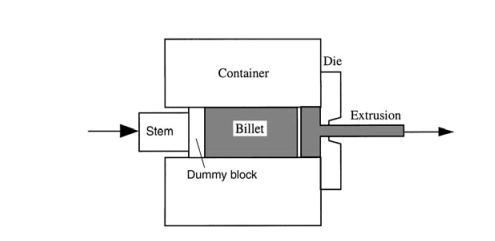
Indirect Extrusion
During indirect extrusion, the die at the forehead of the hollow part travels towards the container, but no relevant displacement between the billet and the container occurs.
Therefore, friction between the billet surface and the container disappears when this process is underway, and no resulting displacement of the billet center in relation to surrounding areas.
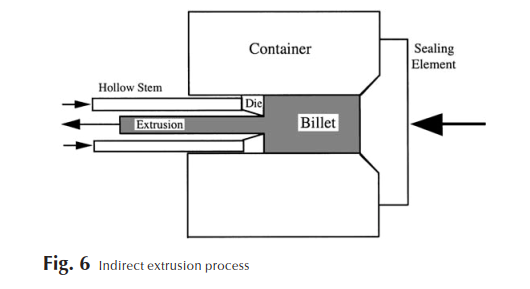
After we introduce so many brilliant idea mentioned above, it’s time to turn the idea into reality, we should know how actual technique works in the smelting industry nowadays.
1. The simple idea of Extrusion:
Put the Billet (compressive metal) in the CONTAINER
- Hold tight the DIE -> Push the Ram
- Here comes out the extruded Bar/Rods
Process Inside:
Extrusion is a diverse deformation process in which a block of metal (billet) is forced to flow by compression through the die opening of a smaller cross-sectional area than that of the original billet.
During the indirect-compression process the reaction of the billet with the container and die results in high compressive stresses that are effective in reducing the cracking of the billet material during pri-mary breakdown from the billet.
The sketches below show the circumstance during the extrusion process:
Use
Extrusion is the best method for breaking down the cast structure of the billet because the billet is subjected to compressive forces only, it can be cold or hot, depending on the alloy and the method.
It is also the best way to produce the metal part in huge amount production which designed with simple format such like water pipe, ventilation duct, etc.
In hot extrusion, the billet is preheated to facilitate plastic defor-mation. Billet-on-billet extrusion:• Solid sections, bars, and rods extruded from solid billets by direct extrusion.
- Tubes and hollow sections extruded from solid billets through port-hole or bridge-type dies (for certain alloys) by direct extrusion.
Tubes and hollow sections extruded from hollow or solid billets (latter pierced in the press via floating mandrel) by direct extrusion.
- Critical solid sections, bars, and rods extruded from solid billets with sealed container through the die mounted on the stem by indi-rect extrusion.
- Tubes and hollow sections extruded from hollow or solid billets (latter pierced in press) via stationary mandrel through the die.